
This means you can now go beyond the aesthetic and performance of plastic parts you are accustomed to getting with traditionally molded parts. With the advancements that have been made in materials science, photopolymers are catching up with thermoplastics. These new photopolymers have the same performance and stability through the entire part lifecycle, which has been the exclusive domain of thermoplastics until now. Using 3D printing (AKA additive manufacturing (AM) or digital production), it is now possible to manufacture complex plastic photopolymer parts without time, costs, and design limitations of thermoplastic tooling. What this means in plain language is “photopolymers can now do the work” for production applications. With the recent advancements in materials science, photopolymer mechanical properties have improved dramatically. We are here to be a resource for you and love doing it, so please don’t be shy. If you have questions at any point, please don’t hesitate to reach out. The volume of SLA print platforms is also attractive to aerospace and energy customers, who are drawn to the casting capability enabled by our SLA QuickCast methodology.īefore I throw too many things at you at once, let’s take a step back and look at what’s possible with SLA materials today that makes it a good match for production, and then shift gears to discuss a few specific options. SLA has found loyal users within the healthcare market, due to its precision and the biocompatibility of select materials, as well as in the automotive market, due to its stiffness and large build sizes, among other properties. The growth in the range of SLA material options has arguably played the biggest role in expanding the range of addressable applications, and the material portfolio continues to grow.
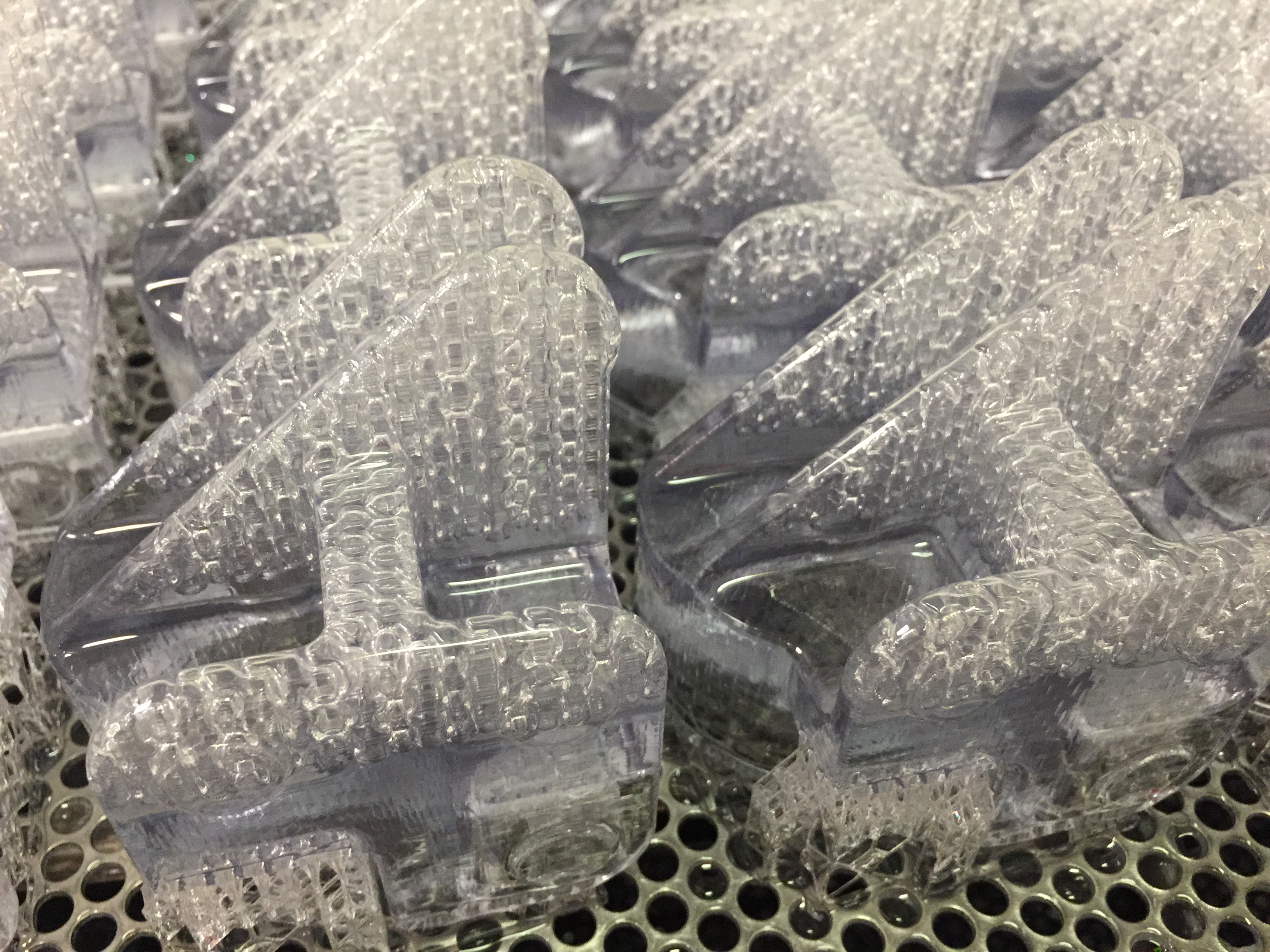
#Quickcast patterns software
In addition to system and software improvements that have been implemented over the years, a major capability shift has occurred in the realm of materials. Since its introduction, SLA has been considered a gold standard for accuracy in 3D printing, and remains such to this day. I consider myself in good company at 3D Systems, where I have had the privilege of spending my career alongside Chuck Hull, also known as the man who started it all with the invention of 3D printing (specifically stereolithography (SLA), the subject of this blog) in 1983. I have been part of the 3D printing industry since the very early days, and now have over 30 years of firsthand experience using and developing this technology. Today’s topic takes a look at another versatile technology in 3D Systems’ portfolio: stereolithography (SLA), and the unique materials and methodologies that are available for production applications.

If you missed part one by David Cullen, it is a great resource on SLS production materials. Welcome to part two of the “Material Information” blog series.
